Classified as a type of positive displacement pump, metering pumps move precise volumes of liquid in predetermined increments within specific time frames. All metering pumps can process water, but some are designed to pump other liquids, like solvents, syrups, solutions, oils, and more. When used to pump chemicals, including acids, slurries, bases, and corrosives, metering pumps may be alternatively referred to as chemical dosing devices.ย Read More…
Since 1886, John Blue has been a trusted pump company for agriculture and industrial applications. With over 136 years of experience, John Blue has gained a reputation as a quality manufacturer of piston metering pumps, 12-volt pumps and chemical injection pumps. We provide dependability and versatility, while serving various industries. John Blue pumps are โGuaranteed To Do The Jobโ.
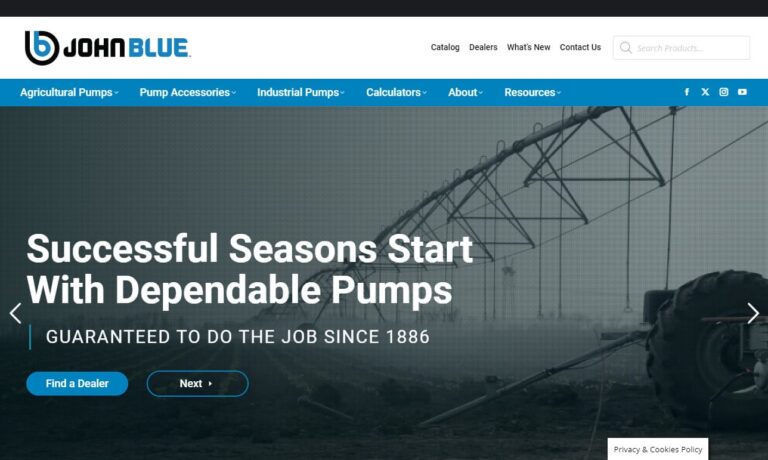
Dewco Controlled Fluid Solutions has been serving industry with fluid metering and control equipment since 1974. With established product lines including metering pumps and solenoid valves among many other products, DEWCO provides quality components for both wholesalers and end users. Our complete system capabilities and repair services mean we can meet your every need quickly and efficiently.
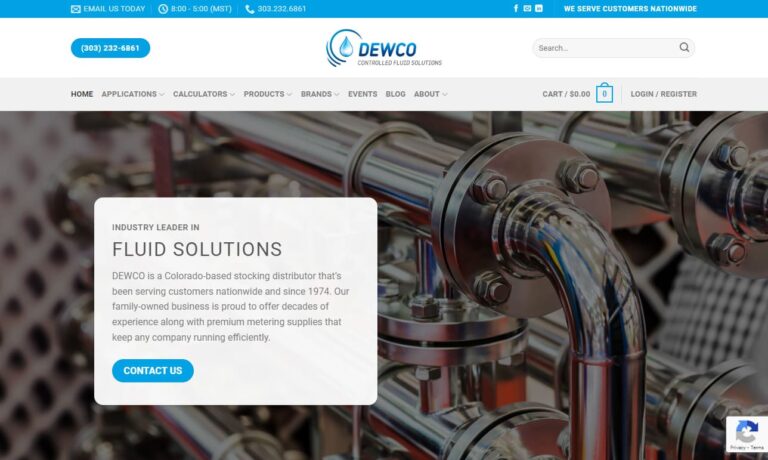
LEWA is your global supplier of metering pumps, process diaphragm pumps and packaged systems. We strive for a close partnership with customers to ensure your complete satisfaction from initial consultation to continuing service and repair, spare parts supply, maintenance and training. A leader in highly precise and high performance pumps, LEWA works with you to find the best component for you.

As one of the oldest manufacturers of metering pumps, Randolph has maintained a loyal following by delivering "rugged, reliable and simple to use" products. Randolph machines all the components of its pumps to its exacting specifications and extrudes its own tubing. The Randolph pump can be found working in industries such as printing, food, pharmaceutical, nuclear and wastewater.
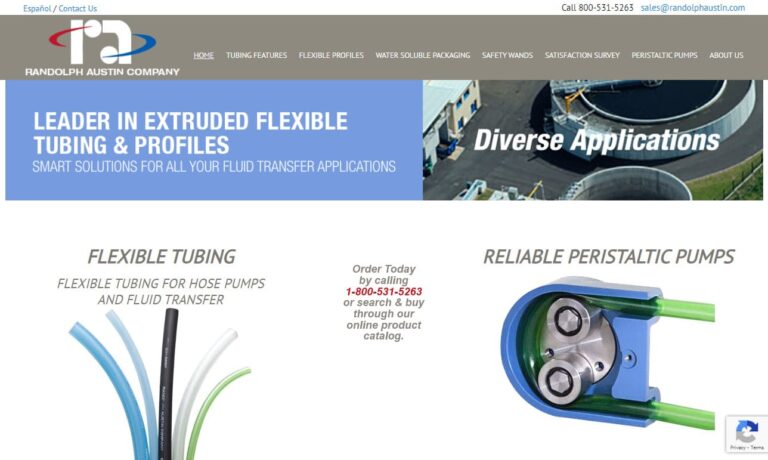
More Metering Pump Manufacturers
Metering pumps, also known as dispensing pumps, controlled-volume pumps, or proportioning pumps, are essential in various industries for their precise and repeatable performance. They cyclically dispense liquid with high accuracy, making them indispensable in many applications. A metering pump delivers small, accurate amounts of liquid into fluid streams. The ideal metering pump achieves delivery accuracy greater than 3% regardless of discharge pressures. This process, known as metering, often involves centrifugal or positive displacement pumps.
While primarily used for water delivery, metering pumps can also handle chemicals, solutions, and other liquids. Their pressure tolerance varies by application, so selecting the appropriate pump for the specific use case is crucial. Industries utilizing metering pumps include commercial vending, food and beverage processing, healthcare, irrigation, laboratory research, chemical engineering, metalworking, milling, pharmaceuticals, plastic fabrication, petroleum and gas, and water treatment.
History of Metering Pumps
Humans have utilized pumps since the era of ancient Rome. The Romans, along with the Indians, Persians, and Egyptians, employed pumps in water wheels to convert water power into energy. The ancient Assyrians likely used water screw pumps for irrigating the Hanging Gardens of Babylon. Many historians attribute the design of the Archimedes screw to the Greek polymath Archimedes, who is believed to have conceived it after visiting Babylon.
During the Dark Ages, pump technology declined but revived in the Middle Ages due to the mining industry’s needs. This led to the invention of the piston pump, or suction pump, which uses atmospheric pressure to remove water from inaccessible areas, aiding mining efficiency. Numerous other pumps were also developed during this time, with “De Re Metallica,” a 1556 work by Georgius Agricola, providing a key reference on 1500s pump technology.
During the Industrial Revolution, new fluid pumps were rapidly developed to meet the demands of steam engines, primarily controlling canal locks and water flow. In 1936, Robert Sheen, with his father Milton Roy Sheen, invented the metering pump in their basement. They founded Milton Roy Pumps, but their early designs allowed leaks and inaccuracies. Later manufacturers improved these pumps by using diaphragms to prevent leaks and incorporating corrosion-resistant materials like PTFE to enhance durability.
In the 1970s, Gorman-Rupp, an Ohio-based company, introduced the first bellows-type metering pump. Around the same time, other manufacturers developed the earliest diaphragm metering pumps with solenoid valves, which allowed for electronic operation. These innovations made the pumps easier to use, maintain, and more cost-effective, while also enabling high-speed operation. Engineers later resolved the high-speed issue by implementing CNC dosing control. Today’s metering pumps leverage advanced technology, providing precision, control, and accuracy.
Metering Pump Design
Manufacturers design metering pumps to meet a variety of specialized needs, offering them in diverse sizes, materials, and configurations. Key design considerations include the fluid composition, maximum discharge pressure, flow rates, temperature ratings, motor capacity, and pump apparatus. Additionally, they must choose between a structure that supports variable displacement at constant speeds or fixed displacement at variable speeds. This choice is influenced by factors such as motor capacity, stroke length, and the extent to which the piston, membrane, or bellows can be extended.
The metering pump comprises a pump head and an electric motor, facilitating the flow of liquid from the inlet line through the pump head and out the outlet line. Most metering pumps allow users to set, adjust, or program the flow rate via various controls such as touchpads, hand dials, or other interfaces.
Metering pumps consist of key components: a cylindrical pump head with an inlet and outlet for fluid flow, a main pump body, various one-way check valves, a pumping mechanism (piston, diaphragm, or bellows), and an electric motor. Tubes or hoses connect the intake check valves to a fluid reservoir and the outlet valve to the pump body, ensuring unidirectional flow. The pumping mechanism, driven by either a manual pedal or a motor, draws in and expels the fluid. The electric motor powers the entire pump head.
Construction of Metering Pumps
All pump types operate slightly differently, but most follow the basic principles of piston pumps. The process begins with the suction or intake stroke, where the piston leaves the pump head chamber. This withdrawal creates a vacuum, opening the inlet valve and drawing fluid into the pump head. When the suction stops, the inlet closes. Next, an operator or motor extends the membrane piston or compresses the bellows, applying pressure to the fluid. This pressure opens the outlet valve, expelling the fluid due to displacement. The rate at which a pump expels fluid is measured in gallons per watt-hour (GPH), reflecting the system’s efficiency.
Metering pumps are categorized based on their flow rate regulation mechanisms. Fixed displacement metering pumps adjust liquid flow according to motor speed, ensuring consistent flow with each rotation, while variable displacement metering pumps maintain consistent liquid flow regardless of motor speed.
Metering Pump Features
Variable displacement constant speed pumps are specialized metering pumps designed to regulate the amount of liquid being pumped by adjusting the stroke, or displacement. These pumps maintain constant flow rates regardless of engine speed, enabling them to deliver a continuous supply of metered fluid. They are integral components in various machines, including drink dispenser systems and dialysis machines, where precise control of fluid flow is essential.
Fixed displacement variable speed pumps adjust the flow rate based on the motor speed rather than the stroke. These pumps, while simpler in design compared to variable displacement pumps, are unable to transfer as much fluid. Despite this limitation, they ensure consistent fluid flow rates with each rotation, making them ideal for use in commercial and industrial settings where reliability is paramount.
Positive displacement pumps are designed to methodically transfer fluids from regions of high pressure to those of lower pressure. These pumps operate by trapping a fixed volume of fluid and mechanically moving it through the pump’s chamber, ensuring a steady, unvarying flow. This mechanism allows for precise control over fluid movement, making them ideal for applications where maintaining a consistent pressure and flow rate is crucial. Whether handling viscous liquids or delicate chemical solutions, positive displacement pumps provide dependable performance, effectively managing the transfer of fluids across diverse industrial processes.
Piston pumps operate using pistons, which are reciprocating, plunger-like cylinders. These pistons move in and out of a corresponding chamber within the pump head to facilitate fluid movement. Both the inlet and outlet valves connect to this chamber, known as the piston chamber. As a positive displacement pump, the piston’s motion displaces liquid. When the piston recedes, it creates a vacuum in the pumping chamber. Once the chamber is filled, the piston moves forward in a discharge stroke, pushing the liquid out of the chamber.
Diaphragm metering pumps, on the other hand, employ a flexible membrane made of materials such as Teflon, rubber, or thermoplastic. These pumps use valves on either side and often rely on hydraulic power to move liquids. The valves can be various shut-off types, including butterfly valves, check valves, or flap valves, tailored to the specific application. One key characteristic of diaphragm pumps is that liquid does not pass through the diaphragm pump valves, effectively sealing the liquid from the extern0al environment. This makes diaphragm pumps an ideal choice for handling sensitive, hazardous, toxic, or noxious fluids, as it prevents leaks. Similar to piston pumps, the diaphragm’s movement creates a vacuum in the chamber, and when the diaphragm expels the liquid, it ensures precise and controlled fluid displacement.
Bellows pumps operate similarly to piston pumps but utilize an accordion-style pleated body to generate positive displacement. These pumps are renowned for their cleanliness and reliability, making them a dependable choice for various applications.
Peristaltic pumps, though less common, feature motor-driven rollers that compress and move liquid through flexible rubber tubing. This mechanism mimics the function of the human gastrointestinal tract, contracting and relaxing to facilitate fluid movement. The peristaltic pump’s hose or tubing dispenses the liquid, with the rollers on the rotor controlling the fluid flow. As the tubing fills, the rotor rotates to shut off the flow, propelling the fluid in the desired direction. This rotation creates a negative pressure within the tubing, drawing in more liquid for continuous pumping.
Pneumatic metering pumps regulate flow rates through the use of pneumatic actuator process signals, allowing precise control over the pumping action. This system relies on the manipulation of air pressure to adjust the flow, ensuring consistent and accurate performance.
Electronic metering pumps, on the other hand, harness electrical currents to power the actuators, thereby facilitating the pumping process. The flow rate in these pumps is modulated using electronic actuator signals. Due to their electronic nature, these pumps can be seamlessly integrated with automated systems and computer programming, providing operators with the ability to control and monitor the pumps remotely and with greater precision.
Micrometer adjustment screw pumps offer a different approach to flow rate control by utilizing micrometer adjustment screws. This method enables fine-tuned adjustments, ensuring that the desired flow rate is achieved with high accuracy and reliability.
Chemical metering pumps are precision-engineered devices specifically designed to handle a variety of chemicals, including bases, slurries, corrosives, acids, and viscous fluids. Also known as chemical dosing devices, these pumps are essential for accurately delivering chemicals into fluid systems. Piston and plunger pumps are commonly utilized in these applications due to their effectiveness in chemical displacement. Maintaining consistent and accurate chemical dosing is crucial, as improper quantities can compromise both the pump’s integrity and the effectiveness of the application.
Fluid transfer pumps, commonly referred to as liquid pumps, encompass any metering pumps designed to move fluids. This category includes pumps of various power sources and flow rate adjustment mechanisms. Among the most prevalent fluid transfer pumps is the water pump, essential in numerous applications for its reliability and efficiency.
Dispensing pumps, another subset of metering pumps, are specifically engineered to dispense a predetermined amount of gas or liquid, ensuring precise and controlled delivery.
Centrifugal pumps, distinct for their ability to move fluids without pulsation or squeezing, achieve this smooth transfer through the action of a revolving disc. This design allows for a continuous and consistent flow, making centrifugal pumps ideal for applications requiring steady fluid movement.
Drum pumps are specialized metering pumps designed to extract fluids from cylindrical containers such as drums, tanks, and barrels. These pumps ensure efficient and precise fluid transfer, making them ideal for applications requiring accurate fluid measurements.
Gear pumps operate by trapping fluid between the teeth of rotating gears. Typically, they use two or three gears in conjunction and are magnetically powered. These pumps are well-suited for applications that demand high pressure, as their design allows for consistent and reliable fluid movement. Gear metering pumps, in particular, are perfect for handling highly viscous liquids due to their capability to withstand high pressures. The intermeshing movement of gears creates a vacuum that facilitates fluid dispensation. This rotary motion enables the liquid to move seamlessly from the inlet valve to the outlet valve, ensuring smooth and controlled fluid transfer.
Small metering pumps are marvels of miniature engineering, blending compact size with exceptional functionality. Despite their small stature and lightweight design, these pumps are adept at handling even the most delicate and precise fluid transport tasks. These diminutive devices excel at delivering fluid with impeccable accuracy and precision, matching the performance of their larger counterparts. Whether in a laboratory setting or a specialized industrial application, small metering pumps provide unparalleled control and reliability, ensuring that every drop is accounted for with exacting detail.
Syringe metering pumps are essential tools in hospitals, valued for their ability to maintain a controlled flow rate. These pumps are primarily utilized to infuse or withdraw liquids with precision. Notably, they are not suited for automated applications and exhibit a high sensitivity to pressure fluctuations, making them ideal for specific medical scenarios requiring meticulous control.
Plunger metering pumps operate by utilizing a plunger to facilitate fluid movement. The process begins with a suction check valve drawing liquid into the chamber. Subsequently, the plunger advances to expel the liquid from the chamber. These pumps are distinguished by their capacity to endure higher pressures and speeds compared to piston pumps, making them robust and reliable for demanding applications.
Solenoid metering pumps harness the power of electromagnetic force to deliver precise and reliable performance. Utilizing an electromagnet, these pumps attract the plunger towards themselves, drawing in the exact amount of liquid required. Designed for ease of operation, solenoid pumps feature integrated LED indicators, simplifying both usage and control. Renowned for their efficiency and simplicity, these pumps provide an optimal solution for various metering applications.
Advantages of Metering Pumps
Metering pumps deliver a host of significant advantages to users. They are distinguished by their ability to dispense fluids with remarkable precision and reliability. Furthermore, they can handle aggressive or dangerous fluids, making them ideal for challenging environments. These pumps are highly adaptable, functioning seamlessly in both high-pressure and low-pressure systems. Moreover, their control options are diverse, enabling users to operate them in various ways depending on the specific design, ensuring maximum flexibility and efficiency.
Applications of Metering Pumps
Metering pumps play a crucial role in various applications, enhancing efficiency and precision. In commercial washing machines, detergent dosing pumps ensure that the correct amount of detergent is delivered with each wash. This not only prevents blockages within the machine but also optimizes the washing process, resulting in consistent and effective cleaning.
In industrial settings, metering pumps are essential for the automated dispensing of raw materials during packaging processes. Their precise control ensures that each product receives the exact quantity required, maintaining quality and consistency across production lines.
Chemical metering pumps are indispensable in water treatment plants, where they introduce accurate amounts of chemicals necessary for water purification. This precision ensures that water is treated effectively, meeting safety and quality standards.
The oil and gas industry also relies heavily on chemical metering pumps. These pumps are used to inject chemicals and gases into pipelines, preventing corrosion and enhancing production rates. By maintaining the integrity of the pipelines, these pumps contribute to the efficient and safe transportation of oil and gas.
Additionally, metering pumps are integral to irrigation systems. They draw water from underground sources, such as ponds or rivers, to irrigate fields and crops. This controlled delivery of water ensures that agricultural operations are both efficient and sustainable, promoting healthy crop growth and optimal water usage.
Metering Pumps Standards
Metering pumps must adhere to various standards based on industry and location. For instance, the American military requires Mil-Spec standards, while the food, beverage, and healthcare sectors in the U.S. mandate FDA compliance. Additionally, it is advisable to ensure metering pumps meet guidelines from organizations such as ATEX, NEMA, or ANSI in the US or EU.
Purchasing Metering Pumps
Metering pumps are indispensable tools for precise fluid management, yet navigating the market to find the right one can be daunting without expert guidance. Achieving optimal performance and reliability hinges on partnering with a reputable metering pump manufacturer. However, the search for such a manufacturer can be equally challenging. To simplify your quest, we have curated a list of trusted metering pump manufacturers, whose information you can find further down this page.
This list is designed to connect you with manufacturers who excel in quality and service. When selecting the ideal manufacturer, consider several factors: Identify which manufacturerโs services best align with your specific requirements. Evaluate the budget-friendly options they offer. Examine their delivery options, including the expected delivery dates. Assess their commitment to providing excellent customer service. By weighing these aspects, you can confidently choose a manufacturer that meets your needs and ensures a seamless and successful acquisition of your metering pump.